Stay focused on truck service by streamlining your shop’s backend processes
The name of the game is fixing trucks. Get them in, get them diagnosed and get them fixed. There’s nothing better than a day that comes together—your technicians churning through work efficiently and safely, and happy drivers, fleet managers and customers. And then there’s the business part—the numbers, the phone calls, the estimates. Funny how
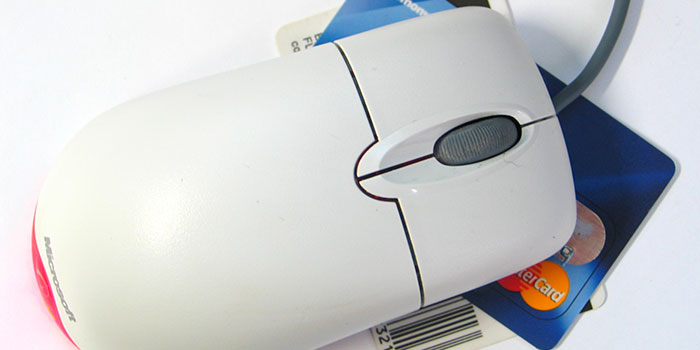
Augmented and mixed reality provide new truck service opportunities
In the field service industry, augmented reality (AR) can play a significant role in changing the way field technicians and the business collaborates to resolve technical issues, provide support and access documentation. Emerging technologies such as AR smart glasses can overlay digital information (such as text, video or audio) onto human field of views, interactively

How heavy-duty product data standards drive truck repair times
Data management is integral to an efficient maintenance operation, but where is your parts data coming from, and how good is it? Simplifying the process reduces errors The parts supply chain is feeding parts information into inventory and maintenance management systems in so many different formats that it could be slowing you down. Not having
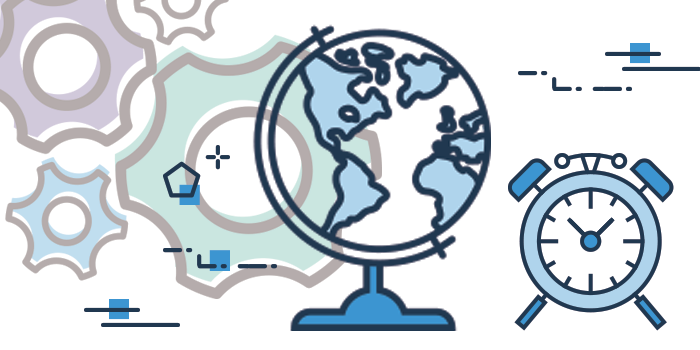
Don’t Call the Customer–Text Them!
The truck is torn down in the service bay, awaiting a customer callback to approve an addition to the original estimate. Three other trucks are in line to be serviced. Unfortunately, there is no easy way to get the disassembled truck back together. The frustrated technician is held up from starting on the other jobs.

How shops are seeing dividends from triage programs
The world moves fast. Many businesses have figured out that their path to the highest profit is to be constantly moving—providing quick shipping, getting products where they need to go and constantly generating revenue. That’s certainly what trucking fleets are looking for—so for them, every second spent in a shop waiting for repairs is not

One-box aftertreatment could mean fewer service issues
Cummins introduced its single module in 2017. This single-can solution incorporates advanced DPF technology, giving customers a larger ash capacity, despite being half the size of old aftertreatment systems. “With the advanced filter, depending on the application, many customers may see extended maintenance intervals,” said Cummins Components Service Engineers Joe Schulz, Mike Bates and Jack

Truck aftertreatment data case study 2
Let’s run this scenario: A regen is needed as a truck is en route to its destination. You coordinate with your fleet manager, dispatch and your driver to schedule the needed regen. Everything has been communicated; you cross it off your to-do list and forget about it—until the truck rolls into one of your bays

Truck aftertreatment service data case study
Both the diesel particulate filter (DPF) and the diesel oxidation catalyst (DOC) are pricey components, but the costs can be compounded if the DOC is left unattended and pushes you to replace the DPF more often than you should be. During aftertreatment service, you’ll want to inspect the DOC and look for evidence of aging,

How heavy-duty truck aftertreatment components can impact each other
While the DPF and DOC are the components we typically associate with aftertreatment service issues, improperly maintained aftertreatment systems can lead to a host of other operational issues. “Issues with the emissions system can have a ‘knock-on’ effect on various components in the engine environment,” said Dr. Barry Southward, vice president of catalyst technology for

What the right data can tell you about aftertreatment issues
You start to realize the power of data analysis when it starts to make your life easier, your decisions clearer. So let’s start with one of your biggest service pain points: aftertreatment systems. The words alone probably makes your stomach sink and your skin crawl, but they don’t have to. With the right data, you
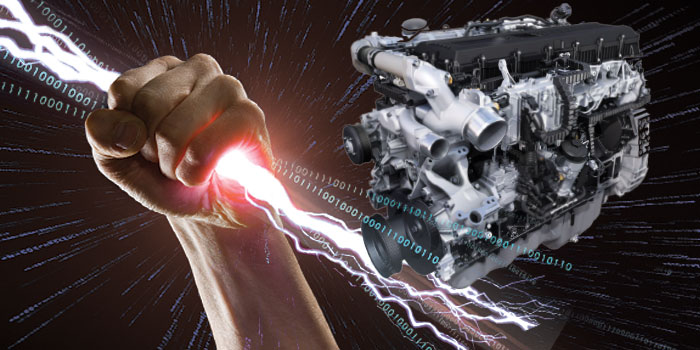
Integrated heavy-duty truck service data
You’re already collecting a huge amount of truck service data—the problem is that it’s often siloed. It’s like filling up four kiddie pools instead of a nicely constructed in-ground pool in the backyard. To improve your service operation, you’re going to need to mix all the data together to see what insight bubbles to the

Quick advice for integrating service data within your fleet
Integrating operational and efficiency data points into your heavy-duty truck service software can make the difference between a heavy-duty truck being down for hours instead of days. Check out this rundown of quick data-centric advice to boost your service process. And click here to read our in-depth integrated truck service data story if you missed
